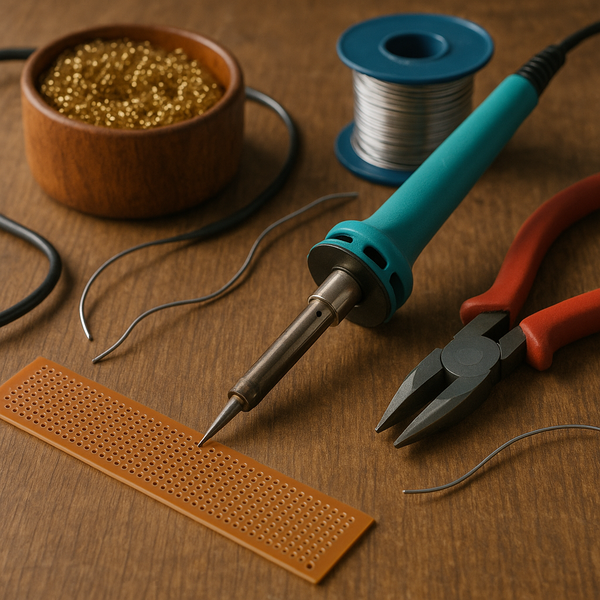
Embarking on the journey of electronics involves mastering fundamental skills, and soldering is arguably one of the most essential. This guide is specifically crafted for newcomers, offering a clear, step-by-step approach to understanding the process. We'll cover everything from the necessary tools to making your very first successful solder joint, ensuring you build a solid foundation for your electronic projects.
Essential Tools for Soldering Beginners
Before you can start soldering, you need the right equipment. Think of it like cooking; you need the right pots and pans. The most crucial item is a good soldering iron. For beginners, a temperature-controlled iron is highly recommended as it prevents overheating components and allows for versatility with different solder types. Look for one in the 30-60 watt range. A soldering iron stand is non-negotiable for safety, providing a secure place to rest the hot iron.
Next, you'll need solder. This is the material that melts to create the electrical and mechanical connection. For electronics, rosin-core solder is standard because the flux within cleans the surfaces as you heat them, allowing the solder to flow properly. Lead-free solder (typically tin/silver/copper alloys) is environmentally friendlier and required in commercial products, but it melts at a higher temperature and can be slightly trickier for beginners. Lead-based solder (like 60/40 tin/lead) melts at a lower temperature and flows easily, making it popular for learning, though proper ventilation is essential due to lead fumes.
Flux is another important chemical agent that cleans metal surfaces and helps solder flow smoothly. While rosin-core solder contains flux, having a separate flux pen or paste can be very helpful, especially when working with components that are difficult to solder. Cleaning the iron tip is vital for effective heat transfer. A damp sponge or, preferably, brass wool (which doesn't cause thermal shock) is used to wipe the tip clean of oxidation and old solder.
Safety glasses are mandatory. Melted solder can splash, and flux fumes can irritate eyes. Proper ventilation is also critical, ideally a fume extractor, especially when using leaded solder. Finally, you'll need wire cutters and strippers for preparing wires, small pliers or tweezers for handling components, and possibly a "helping hands" tool to hold components or wires while you solder.
Prioritizing Safety First
Soldering involves high temperatures and potentially hazardous materials, so safety must always be your top priority. Always wear safety glasses to protect your eyes from splashes of molten solder or clipping wires. Work in a well-ventilated area to avoid inhaling solder fumes. If you don't have a fume extractor, open a window or use a fan to direct fumes away from you. Never touch the hot tip of the soldering iron or the barrel; they can cause severe burns. Always return the iron to its stand immediately after use.
Be mindful of where hot solder drips might fall. Use a heat-resistant mat if working on a surface that could be damaged by heat. When clipping wires or component leads, position yourself so the cut pieces don't fly into your face or eyes. Ensure the soldering iron cord is positioned safely so it doesn't get in your way or accidentally pull the iron off the bench.
Getting Started: Preparation Steps
Good preparation is key to successful soldering. Start by ensuring your workspace is clean, well-lit, and free of flammable materials. Gather all the tools and components you will need. If you're working with a circuit board, familiarize yourself with the component placement.
Prepare the surfaces you intend to solder. This is often called "tinning". For wires, twist the strands together tightly and apply a small amount of solder to the tip of the iron, then touch it to the twisted wire until the solder flows and coats the strands. For component leads, if they are oxidized (look dull rather than shiny), you might need to gently scrape them clean before applying a tiny amount of solder. For circuit boards, the pads are usually pre-tinned, but they must be clean. If they look dirty, you can gently scrape them or use a bit of flux.
Plug in your soldering iron and wait for it to reach its operating temperature. If you have a temperature-controlled iron, set it appropriately for the solder you are using (check the solder packaging for recommendations, typically 300-400°C or 570-750°F). Once hot, clean the tip on your sponge or brass wool and apply a small amount of fresh solder to the tip. This process, also called tinning the tip, helps protect the tip from oxidation and improves heat transfer.
Making Your First Solder Joint
Now for the main event! The goal is to heat *both* the component lead and the pad on the circuit board simultaneously, then apply solder to the *heated surfaces*, not the iron tip. Position the component lead through the hole in the circuit board pad. If needed, gently bend the lead on the underside to hold the component in place.
Bring the clean, tinned tip of the soldering iron into contact with both the component lead and the pad at the same time. Ensure good physical contact to transfer heat efficiently. Hold the iron there for just a couple of seconds to allow the heat to spread. Then, touch the tip of the solder wire to the junction where the iron is heating the lead and the pad. The solder should melt instantly and flow smoothly around the joint, covering the pad and forming a small, shiny cone shape up the component lead. Use only enough solder to create this connection – too much can lead to cold joints or bridges between pads.
Once the solder has flowed properly, remove the solder wire *first*, then immediately remove the soldering iron. Avoid moving the component or board while the solder is cooling and solidifying (this only takes a second or two). A good solder joint will look shiny and have a slightly concave shape, like a mini volcano. It should not be dull, lumpy, or spherical (these indicate a cold joint or not enough heat/flux).
Troubleshooting Common Issues
You'll likely encounter a few challenges when you're starting out, and that's perfectly normal. One common problem is a "cold joint," which looks dull, grey, and lumpy. This happens when the joint wasn't heated enough or there was movement while the solder was cooling. To fix it, simply re-heat the joint carefully and add a tiny bit more solder if needed, ensuring the lead and pad are hot before applying solder.
Another issue is solder bridges, where solder accidentally connects two adjacent pads or leads that shouldn't be connected. This often happens with too much solder or poor technique. To fix a bridge, you can often use a clean, hot iron tip to drag the excess solder away, or use desoldering braid (a flux-infused copper wick) or a desoldering pump (solder sucker) to remove the excess solder.
Components can get damaged by excessive heat. This is why temperature control and working quickly are important. If a component lead seems resistant to soldering, it might be oxidized. Ensure you have proper flux and are cleaning the surfaces and your iron tip correctly. Practice on scrap materials before working on a valuable project.
Beyond the Basics: What's Next?
Once you're comfortable making basic solder joints, you can explore more advanced techniques like desoldering components with multiple pins (like integrated circuits), soldering surface-mount components (which are much smaller and sit on top of the board), and using different types of solder and flux. Experimenting with different projects, from simple LED circuits to more complex microcontrollers, will further hone your skills. Soldering is a craft that improves with practice, so keep building and learning!
Soldering is a fundamental skill that opens up a world of possibilities in electronics. By starting with the right tools, prioritizing safety, preparing your workspace, and practicing the basic technique, you can quickly become proficient. Don't be discouraged by imperfect joints at first; learning takes time and repetition. With patience and persistence, you'll soon be confidently connecting components and bringing your electronic ideas to life.